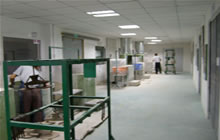 |
Shell (1): Area: This is the shell room, constant temperature
control for year-round to build up the best condition to dry the
shell. |
 |
Shell(2): Dipping: Design the most suitable
dipping procedure according to the different product
construction and make the shell mold accordingly.
|
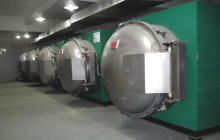 |
Shell(3): Drying: For the first two layers of dipping and stuccoing
would be dried by traditional drying process which is through the
air and must be in a constant temperature control area. |
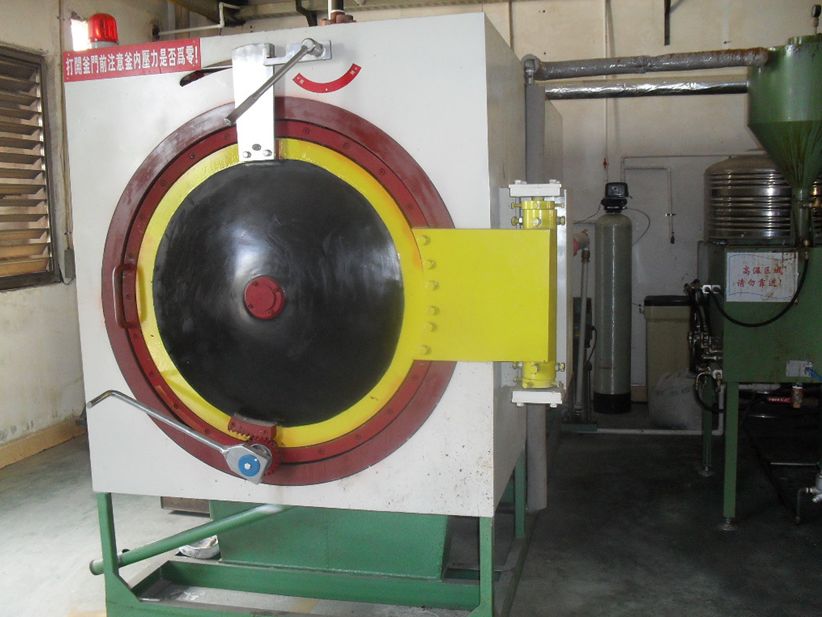 |
Shell (4): Vacuum drying system: Have you seen this drying system
in any other casting foundries? We have the ambition to equal or
even surpass our competitor, with this innovate change; we could be
the only one who use vacuum drying system in investment casting
industry. This will shorten the drying lead time from 7 days to 2
days compared with the air drying process. |
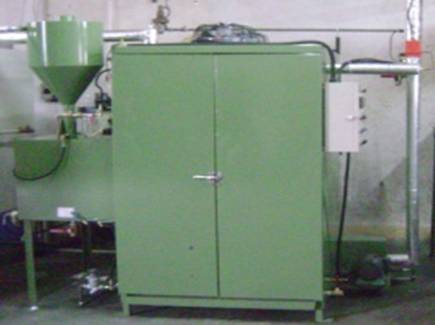 |
Shell (6): De-wax: the last production process of shell building.
Steamer is the traditional way for de-wax, however it is not a good
choice to the environment. Therefore, we use electronic thermal
de-wax process to make less pollution and it¨s better to the
environment. |